高效能智能生产软件全方位驱动企业创新升级
adminc2025-03-30软件教程60 浏览
1. 传统工厂真的会被智能软件取代吗?
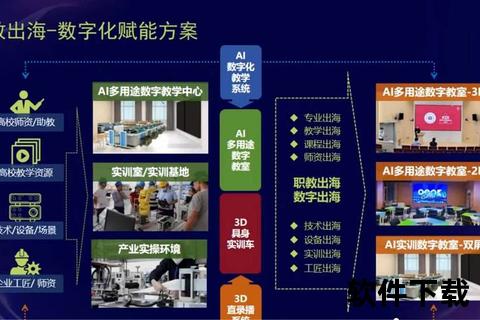
“机器换人”的争议在制造业从未停歇:一边是沿海工厂用智能软件将生产效率提升200%的案例频现,另一边是中小企业主抱怨“数字化投入像无底洞”。这种撕裂背后,隐藏着一个更本质的问题——高效能智能生产软件究竟是颠覆传统的破坏者,还是产业升级的加速器?
某汽车零部件企业曾陷入典型困境:价值800万的进口设备因系统不兼容,每天有3小时处于停机状态。引入智能生产调度系统后,设备利用率飙升到92%,订单交付周期缩短40%。这个案例揭示了一个真相:高效能智能生产软件全方位驱动企业创新升级,本质上是用数字神经重构生产逻辑。
2. 如何让机器学会“思考”?
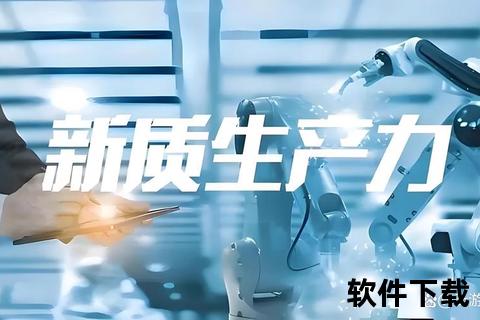
在双星轮胎的“工业4.0”工厂,300台智能机器人组成的生产网络,能根据订单变化自动调整工艺流程。其秘诀在于搭载了具备自学习能力的MES系统:
设备健康监测模块实时采集2.7万组振动数据,提前48小时预警轴承故障
工艺参数优化算法每月迭代12次,使轮胎动平衡合格率提升至99.97%
能耗管理系统通过热力学模型,每年节省电力成本230万元
这种“软件定义制造”的模式正在重塑产业链。航天科工集团的云雀协同研发平台,让分布在8省的设计团队能同步修改三维模型,使某型无人机研发周期从18个月压缩至11个月。高效能智能生产软件全方位驱动企业创新升级,正从单点突破转向生态重构。
3. 数据流动如何创造真金白银?
格力电器与华为合作的5G智能工厂给出示范:
1. 生产环节:视觉检测系统识别精度达0.02mm,替代30名质检员
2. 物流环节:AGV调度算法将仓储周转率提高35%
3. 决策环节:需求预测模型使库存水位下降28%
更惊人的是设备联网带来的增值服务。某机床企业通过在设备植入智能控制模块,不仅实现远程运维,更衍生出按加工件数收费的新模式——客户单位产量成本降低15%,厂商服务收入增长40%。这种双赢局面印证了:高效能智能生产软件全方位驱动企业创新升级,本质是数据资本的价值释放。
4. 转型阵痛期怎样平稳渡过?
宁波某服装厂的数字化转型堪称教科书:
首年投入200万改造5条智能生产线,专注解决裁剪工序15%的物料浪费
次年引入AI排产系统,将订单响应速度提升至48小时
第三年搭建数字设计平台,实现2000款样衣的云端协同开发
这种“小步快跑”的策略,让企业用三年时间完成利润率从3.2%到8.7%的跨越。与之形成对比的是,某急于求成的机械厂一次性投入1500万建设“智能工厂”,却因人才断层和管理惯性,导致系统上线半年仍无法正常运转。
行动指南:
1. 诊断核心痛点:用价值流图找出损耗超过20%的关键环节
2. 选择敏捷方案:优先考虑支持模块化扩展的SaaS平台
3. 培养数字工匠:设立“人机协同专员”岗位衔接新旧体系
4. 构建数据闭环:确保每个改进动作都能量化验证
当东莞的电子厂主用手机查看实时产能,当山西的煤矿工人通过AR眼镜获得维修指引,这些场景揭示的不仅是技术变革,更是中国制造向“智造”跃迁的底层逻辑。高效能智能生产软件全方位驱动企业创新升级,最终指向的是这样一个未来:每个生产决策都有数据支撑,每次技术迭代都创造新价值,每条产业链都具备自进化能力。